中國航發:航空裝備激光增材制造技術發展及路線圖
增材制造從三維模型出發實現零件的直接近凈成形制造。相比傳統的減材制造,增材制造將多維制造變成簡單的由下而上的二維疊加,降低了設計與制造的復雜程度。航空裝備領域目前涉及的增材制造主要是金屬材料增材制造,已發展出激光增材制造、電子束增材制造和電弧增材制造三類增材制造技術。
激光增材制造是當前航空裝備領域最具代表性的增材制造方法,主要包括以粉床鋪粉為技術特征的激光選區熔化和以同步送粉為技術特征的激光直接沉積。激光選區熔化工藝熱輸入小、成形尺寸精度高,適合制造航空發動機噴嘴、渦流器等復雜結構零件以及拓撲點陣等新型結構;激光直接沉積工藝效率較高、力學性能較好,但制造精度不高,適合制造飛機框梁等重要承力結構。由于國內外對激光增材制造技術非常重視,其技術發展迅速,陸續應用于飛機和航空發動機的制造,并且呈現出快速增長的趨勢。
為了更好地把握增材制造的發展現狀和趨勢,提前做好航空領域增材制造技術發展的戰略布局,推進增材制造在航空領域的發展與應用,本文針對激光增材制造最近幾年的發展,開展文獻、資料、信息的搜集、整理、分析。在對增材制造現狀和發展趨勢分析的基礎上,提出2035年航空領域增材制造技術發展目標和相應的政策和環境支撐、保障需求,并嘗試給出 2035 年技術發展路線圖建議。
1.激光增材制造的工藝原理及特點
激光選區熔化(SLM)基于分層疊加制造原理,利用高能量激光束逐層熔化金屬粉末成形復雜結構金屬零件。圖1為激光選區熔化示意圖。SLM在已有的 3D 模型切片數據的輪廓數據基礎上,生成填充掃描路徑,設備按照這些填充掃描線,控制激光束選區熔化各層的金屬粉末材料,逐步堆疊成三維金屬零件。
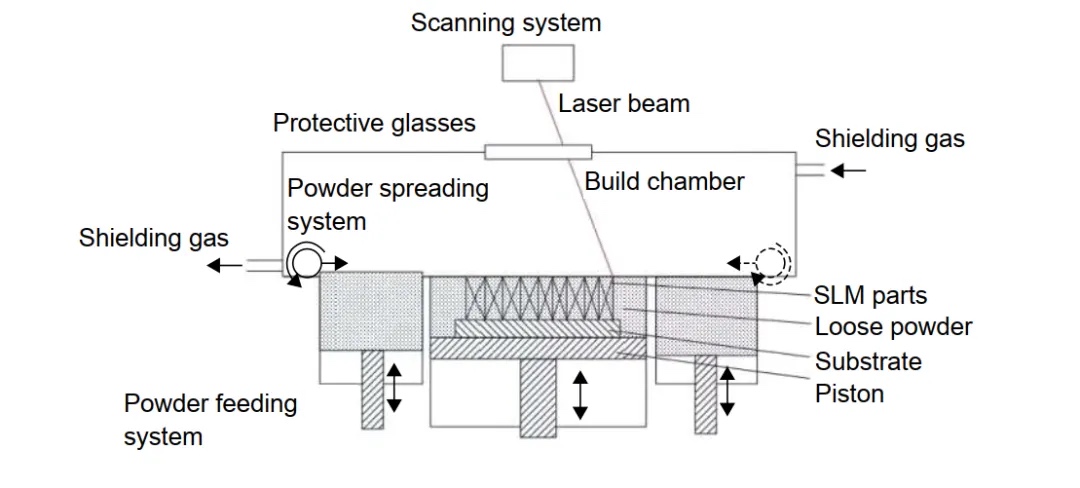
激光選區熔化技術具有以下特點:(1)成形原料一般為一種金屬粉末,主要包括不銹鋼、鎳基高溫合金、鈦合金、鈷-鉻合金、鋁合金以及貴重金屬等;(2)采用細微聚焦光斑的激光束成形金屬零件,成形的零件精度較高,表面稍經打磨、噴砂等簡單后處理即可達到使用精度要求;(3)成形零件的力學性能較好,一般拉伸性能可超鑄件,達到鍛件水平;(4)高向沉積速度較慢,導致成形效率較低,零件尺寸會受到鋪粉工作箱的限制,不適合制造大型的整體零件。
激光選區熔化的局限性主要表現在:(1)由于激光器功率和掃描振鏡偏轉角度的限制,設備能夠成形的零件尺寸范圍有限,目前整體制造 800 mm以上尺寸零件的設備不夠成熟;(2)加工過程中,容易出現翹曲,還容易因粉末熔化后不能均勻地鋪展于前一層發生球化現象;(3)成形體結構密度控制效果不好,難以承受高載荷的結構效應。
激光直接沉積工藝如圖2所示。激光從熔覆頭頂部沿軸線方向向下射出,經聚焦鏡匯聚在粉末聚焦點附近,將同步出射的粉末熔化;同時,熔覆頭或工作臺按每層圖形的掃描軌跡移動,熔化的金屬液就在基體或上一層凝固層基礎上完成一層實體的成形;計算機繼續調入下一層圖形掃描數據,重復上述動作,如此逐層堆積,最終成形出一個具有完全冶金結合的金屬零件。
激光直接沉積技術具有以下特點:
(1)無需模具,可實現復雜結構的制造,但懸臂結構需要添加相應的支撐結構;
(2)成形尺寸受限制小,可實現大尺寸零件的制造;
(3)可實現不同材料的混合加工與梯度材料制造;
(4)可對損傷零件實現快速修復;
(5)成形組織均勻,具有良好的力學性能,可實現定向組織的制造。
激光直接沉積技術的局限性主要表現為:
(1)成形時熱應力較大;
(2)成形精度不高;
(3)所得金屬零件尺寸精度和表面粗糙度都較差,需較多的機械加工后處理才能使用。
目前激光選區熔化主要應用于小尺寸或中等尺寸復雜精密結構的精確近凈成形增材制造,結構的功能屬性一般大于承載屬性。
激光直接沉積主要用于中等或大尺寸復雜承力結構的增材制造,結構的承載屬性一般大于功能屬性。
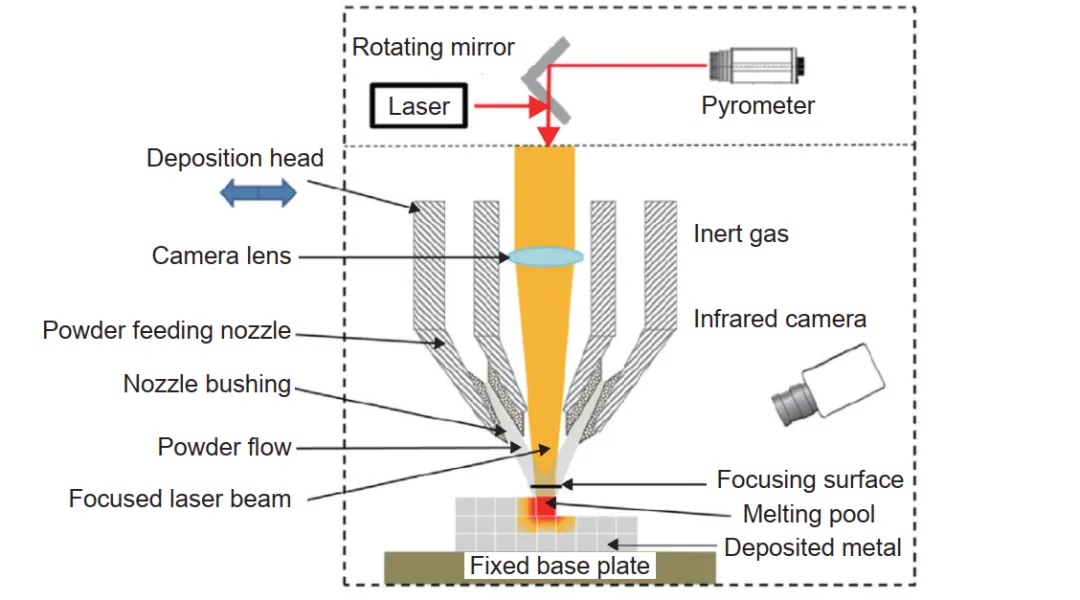
2.國外激光增材制造技術發展現狀和趨勢
2.1 工藝研究
2.1.1 激光選區熔化
激光選區熔化對粉體材料的要求為:
尺寸在15~60μm的金屬顆粒群,并盡可能同時滿足純度高、少或無空心、衛星粉少、粒度分布窄、球形度高、氧含量低、流動性好和松裝密度高等要求。通過近 30 年的發展,國外成功采用真空感應氣霧化法(VIGA 法)、無坩堝電極感應熔化氣體霧化法(EIGA 法)、等離子旋轉霧化法(PREP 法)以及等離子火炬法(PA 法)等制備 SLM 增材制造專用粉體材料,已經具備成熟穩定的批量供貨能力,并壟斷了全球大部分SLM增材制造專用粉體材料市場。
在成形工藝研究方面,波音、洛克希德-馬丁、諾斯羅普-格魯曼、通用動力、GE、霍尼韋爾、派克-漢尼汾等公司已利用激光選區熔化技術開發出商業化的金屬零部件。在SLM成形過程中伴隨著復雜的物理、化學、冶金等過程,容易產生球化、孔隙、裂紋等缺陷。白俄羅斯科學院研究了金屬粉末球化形成的具體過程,指出球化主要會形成碟形、杯形、球形 3 種典型的形狀,并分析了各自形成的機理。德國魯爾大學研究了不銹鋼粉末激光選區熔化成形的相對密度與工藝參數的關系,發現高的激光功率有利于成形出高密度的金屬零件,低的掃描速率有利于掃描線的連續,促進致密化。英國利茲大學對不銹鋼和工具鋼合金粉末進行了SLM研究,分析了掃描速率、激光功率和掃描間隔對成形件質量的影響。
國外對增材制造工藝研究非常細致,例如,德國某設備商為開發一種新粉末(可用粒度為20~60 μm)的激光選區熔化工藝,往往需要6~8個月的工藝摸索,涉及的參數多達70余項。
國外已將拓撲優化設計與輕量化技術應用于SLM增材制造,實現了由“ 制造引導設計、制造性優先設計、經驗設計” 的傳統設計理念向“ 設計引導制造、功能性優先設計、拓撲優化設計” 的增材制造設計理念轉變。
支撐設計方面,國外已經應用無需線切割即能分離打印件與基板的特殊支撐設計技術,大大縮短了取件周期。
在后續熱處理技術方面,2002年美國汽車工程師協會發布了第1個增材制造技術標準《退火Ti- 6Al-4V鈦合金激光沉積產品》,至今已陸續頒布了19項標準。這些標準涵蓋了產品的退火和熱等靜壓、消除應力退火以及退火或熱等靜壓后的時效制度,反映國外已經在控制內部缺陷、消除殘余應力、減少變形等方面開展了大量的研究工作。
航空航天等領域對增材制造零件表面粗糙度有較高的要求,金屬增材制造零件的后續光整加工不可或缺。磨粒流加工方法具有高加工可達性,對復雜內腔結構進行光整加工具有顯著的優勢。采用磨粒流拋光增材制造零件,對由“ 階梯效應” 導致的粗糙表面具有良好的改善效果。國外研究發現,采用磨粒流加工拋光SLM制造的葉片,沿流動方向存在明顯的拋光不一致性,葉片進排氣邊的拋光效果明顯好于葉盆及葉背中心區域,葉片型面精度降低。
2.1.2 激光直接沉積
激光直接沉積增材制造對粉末的要求為:粒度分布一般在45~420μm范圍內,同時盡可能滿足純度高、少或無空心、衛星粉少、球形度高、氧含量低、流動性好和松裝密度高等要求。粉末制備推薦采用電極感應熔化高純氬氣霧化或等離子旋轉電極法。
激光直接沉積技術效率高,成形零件的尺寸大,還可在原有零件上進行修復和再制造,但缺點是不具備制造復雜空心結構的能力,成形的毛坯還需要經過較多的機械加工才能獲得最終零件。值得指出的是,激光直接沉積方法還能同步混合不同材料的粉末來實現復合材料的成形。
1995年起,美國約翰霍普金斯大學、賓夕法尼亞州立大學和MTS公司共同開發了利用大功率CO2激光器實現大尺寸鈦合金零件的制造技術,并合作成立了AeroMet 公司,實現了Ti-6Al-4V合金1~2kg/h的沉積速率。
對于激光直接沉積技術的研究主要從成形工藝和成形組織性能兩方面展開。美國的Sandia國家實驗室和Los Alomos國家實驗室針對鎳基高溫合金、不銹鋼、鈦合金等金屬材料進行了大量的激光直接沉積成形研究,所制造的金屬零件不僅形狀復雜,且其力學性能接近甚至超過傳統鍛造技術制造的零件。瑞士洛桑理工學院深入研究了激光快速成形工藝參數對成形過程穩定性、成形零件的精度、顯微組織以及性能的影響,并將該技術應用于單晶葉片的修復。
增材制造材料的顯微組織是由移動熔池中熔體的冶金動力學行為與晶體形核/長大機制決定的,激光直接沉積技術在材料顯微組織控制方面具有較大的自由度,早在2001年Gäumann等就實現了單晶與多晶鎳基高溫合金的調控,而 Liu等通過送粉量與激光功率的匹配實現了具有等軸晶與柱狀晶混合組織鈦合金的成形。
激光直接沉積成形過程中隨著高能激光束長時間周期性劇烈加熱和冷卻、移動熔池在池底強約束下的快速凝固收縮及其伴生的短時非平衡循環固態相變,會在零件內部產生極大的內應力,容易導致零件發生嚴重變形、甚至開裂。
美國國家航空航天局 (NASA) 噴氣推進實驗室開發出一種新的激光金屬直接成形技術,可在一個部件上混合打印多種金屬或合金,解決了長期以來飛行器零部件制造中所面臨的一大難題——在同一零件的不同部位具有不同性能。
德國DMG MORI旗下的Lasertec系列,整合了激光增材制造技術與傳統切削技術,不僅可以制造出傳統工藝難以加工的復雜形狀,還改善了增材制造過程中存在的表面粗糙問題,提高了零件的精度。
2.2 工藝設備
經濟、高效的設備是激光增材制造技術廣泛推廣和發展的基礎。目前,激光選區熔化增材制造設備的研究主要集中在德國、法國、英國、日本、比利時等國家。激光直接沉積增材制造設備的研究主要集中在美國、德國等國家。
2.2.1 激光選區熔化增材制造設備
激光選區熔化SLM技術及設備研究起步最早的國家當屬德國,其技術也比較成熟 。
德國EOS公司是全球最大,同時也是技術較為領先的激光選區熔化增材制造成形系統制造商。
目前EOS設備主要有EOSINT M280、M290和M400三款。EOSINT M280激光燒結系統采用Yb-fibre激光發射器,高效能、長壽命,光學系統精準度高。根據IDTechEx的數據,M280曾用于制造當前GE航空發動機LEAP的噴油嘴。
為全面取代EOS M280,EOS公司推出升級版的增材制造設備EOS M290。EOS M290提升了過程監控能力,尤其適合航空航天和醫療等高精尖行業的要求。除此之外,EOS M290在其他方面也做了一些改進。EOS M290增材制造設備的新增功能包括:
(a)EOSTATE PowderBed,一個內置在構建腔室的攝像頭,通過靜止圖像監視粉末床上的粉末沉積狀況。
(b)EOSTATE Base,統一監控一系列參數,包括Z軸或掃描儀的位置、激光功率、空氣濕度、溫度和壓力。
(c)EOSTATE LaserMonitoring,檢測在整個構建期間的激光功率。該系統配備有一個400W的激光,該激光具備高輻射品質和穩定的性能。
(d)EOS ParameterEditor,用戶可以使用它修改一系列的曝光參數。該工具使客戶能夠在EOS參數集的基礎上根據具體應用開發自己的參數,包括激光功率和曝光速度或策略。參數編輯器的更新版本正在開發中,新版本的參數編輯器還可以修改層厚度、惰性氣體流、構建平臺的溫度等。
EOS M400是EOS公司尺寸最大的金屬選區熔化設備,也是目前市場上較為成熟的大尺寸選區熔化設備,其最大成形尺寸為400mm×400mm×400mm。該設備采用1kW的光纖激光器及雙向鋪粉方式,可以有效提高成形效率;同時設備集成了監控系統,可對鋪粉情況、Z軸位置、激光功率、濕度、溫度、壓力等參數進行監控,保證成形過程的穩定和產品的可追溯性。
目前國際上主要SLM裝備的技術指標如表1所示,其中Concept Laser公司生產的SLM裝備可成形的零件尺寸最大,EOS公司生產的SLM裝備可成形的零件尺寸次之,但是EOS公司生產的M系列SLM裝備的商用化成熟度最高,應用最廣。
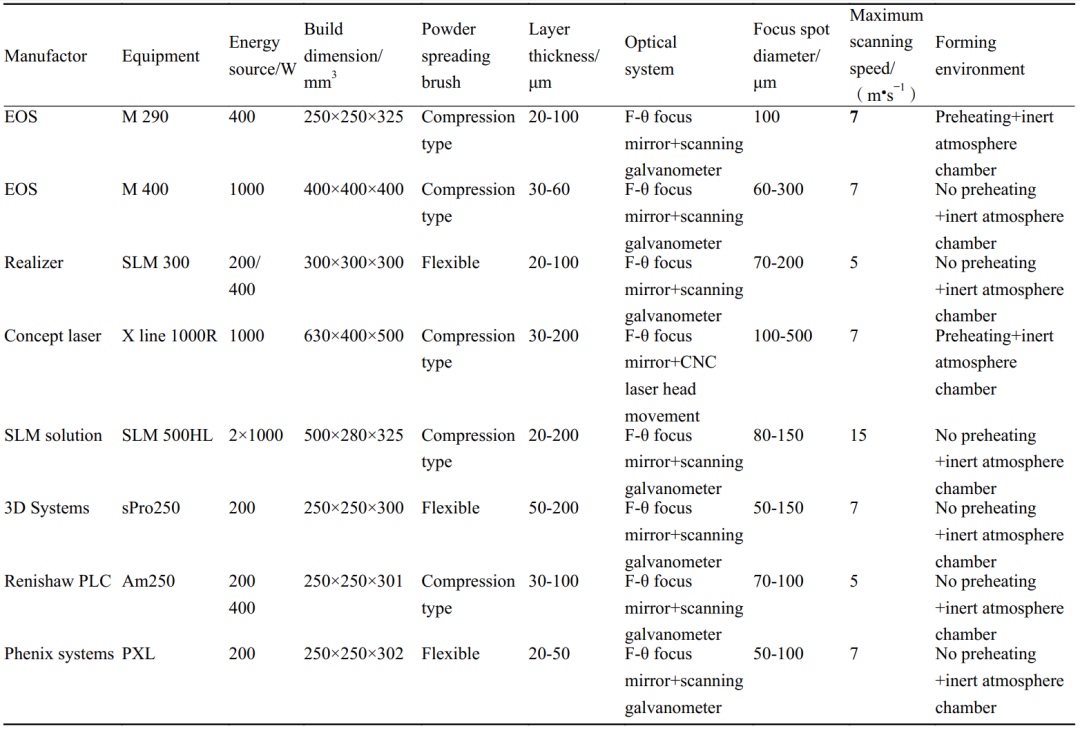
2.2.2 激光直接沉積設備
在激光直接沉積設備制造研究方面 ,美國EFESTO公司堪稱大尺寸3D金屬打印專家。該公司推出典型設備為大型的同步送粉激光增材制造設備EFESTO 557,該設備擁有一個1500mm×1500mm×2100mm的超大工作室。
美國Optomec公司推出的激光直接沉積設備型號為LENS 850-R,該設備擁有一個900mm×1500mm×900mm的超大工作室,并配有5軸移動工作臺,最大成形速度為8.19cm3/min。
德國阿諾德激光系統制造有限公司推出的激光綜合加工系統,也是國際上一款主流的激光直接沉積增材制造設備。
國際上近些年還推出了增減材復合加工設備和技術。
日本DMG公司 (DMGMORI) 推出的LASERTEC653Dt331,配有2kW的激光器,可進行激光直接沉積,輔以全功能的高剛性單體結構的5軸聯動數控銑床進行高精度的銑削加工,構成獨特的混合加工機床,最高可比普通粉床中成形速度快20倍,并允許直接銑削最終零件中無法達到的加工部位。
日本Mazak公司也推出了增減材復合制造裝備。其典型設備INTEGREX i-400AM能夠進行全面的五軸車銑復合加工,B軸擺動幅度在-30°~+210°之間,同時配置了全C軸分度車削主軸及可編程尾座。
2.3 技術應用
激光增材制造技術最早于2001年開始應用于美國的艦載殲擊機中,通過鈦合金增材制造技術生產出飛機的承力結構件。2011年英國的南安普頓大學通過增材制造技術生產出包括無人機的機翼、控制面板和艙門的整體框架。
2012年之后,鈦合金增材制造技術在航空領域的應用取得前所未有的發展,鈦合金零件不僅在飛機制造中得到廣泛的應用,而且新型的鈦合金材料開始在火箭、航天飛機等航天裝備中得到應用。
鈦合金增材制造技術生產的零件大大減少了航天設備之間的焊縫數量,由于鈦合金的強度更高,使得航天設備的安全性大大提高。
NASA馬歇爾航天中心采用激光增材制造技術制備大量的火箭發動機零件,包括發生器導管、旋轉適配器等。激光增材制造的RS-25火箭發動機彎曲接頭,與傳統設計相比,減少60%以上的零件數量、焊縫以及機械加工工序。NASA還提出AMDE計劃,對增材制造技術在氫氧發動機整體化設計制造中的應用進行驗證。與傳統制造方法相比,采用增材制造技術設計制造的氫氧發動機零件總數減少80%。
法國泰雷茲阿萊尼亞宇航公司將激光直接沉積制造的鋁合金大尺寸遙測及指令天線支撐零件應用于Koreasat5A和Koreasat7通信衛星的制造。零件已經通過振動驗收測試,展示了很好的動態特性重復性。使用增材制造技術可減重22%,縮短生產時間1~2 個月,節省經費約30%,并可提高產品的性能。
基于激光增材制造工藝的結構拓撲優化設計在航天領域得到應用。結構拓撲優化技術與激光增材制造工藝相結合,可以發揮出激光增材制造工藝在零件輕量化制造方面的最大優勢,同時能夠實現拓撲優化結構的制造。空中客車防務與宇航公司英國分部采用激光增材制造技術制備了歐洲航天局Eurostar E3000的鋁合金支架(圖3),用于安裝遙測和遙控天線。通過拓撲優化以及激光增材制造工藝,實現原本由4個零件通過44個鉚釘連接而成支架結構的整體制造,并且通過優化設計,在實現35%減重的同時使結構剛度提高40%。該鋁合金支架已經完成質量檢測,具備衛星裝載飛行的資質。
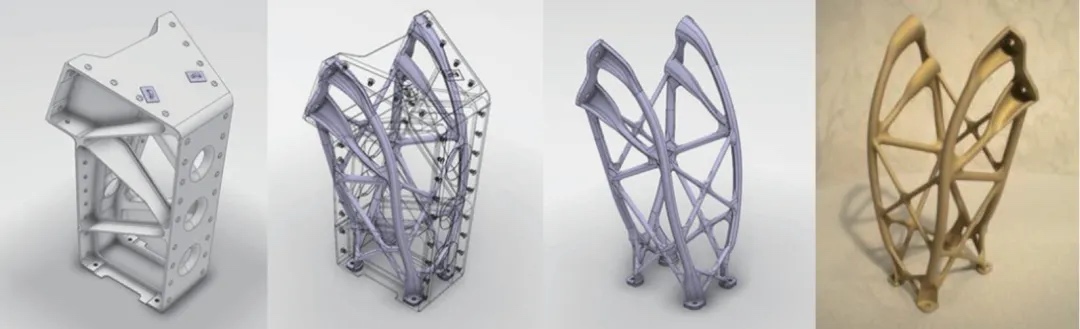
2012年,GE公司收購了Morris公司以及其兄弟公司Rapid Quality Manufacturing。這兩家公司均是增材制造領域的佼佼者,同時也是GE 公司下一代LEAP發動機的零部件供應商。收購Morris公司后,GE立即開始探索增材制造技術的極限,尋找新的應用點。GE商用發動機獲得FAA批準的首個增材制造零件為高壓壓氣機溫度傳感器(T25)外殼(圖4)。T25傳感器外殼由鈷鉻合金制造,保護溫度傳感器脆弱的電子器件,防止其結冰以及被急速氣流損壞。T25傳感器外殼于2014年10月完成最終設計,2015年2月獲得FAA認證,在第二周就投入使用。2015年4月G公司宣布,該公司有超過400臺GE90-40B發動機加裝了用增材制造技術生產的 T25傳感器外殼。GE航空公司還采用激光增材制造技術制造了新一代的LEAP噴氣發動機燃油噴嘴(圖5),并于2015年服役。
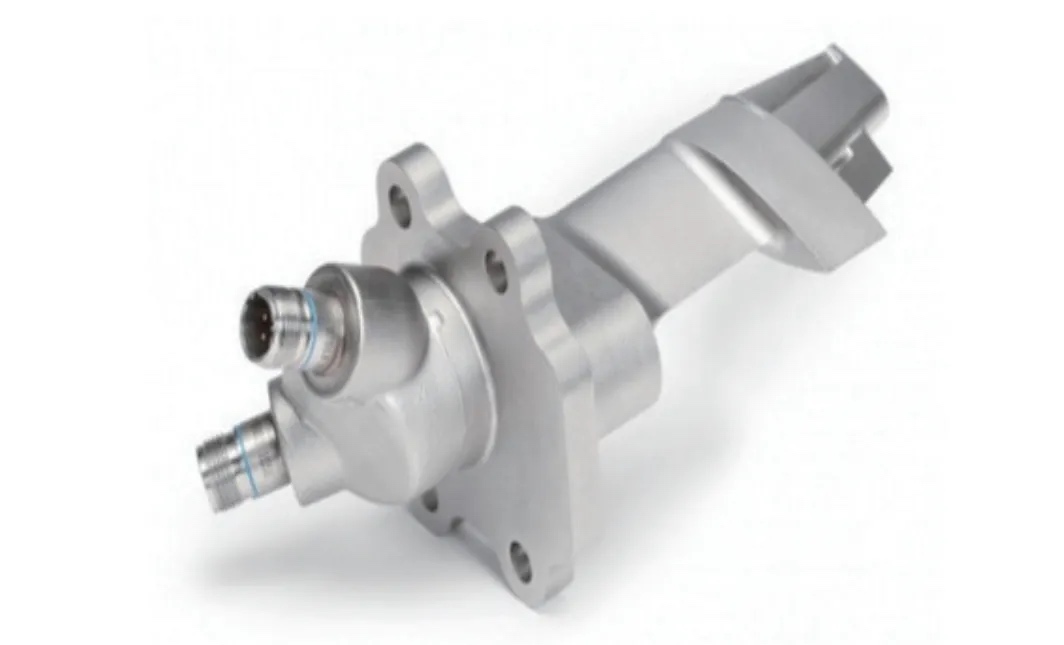
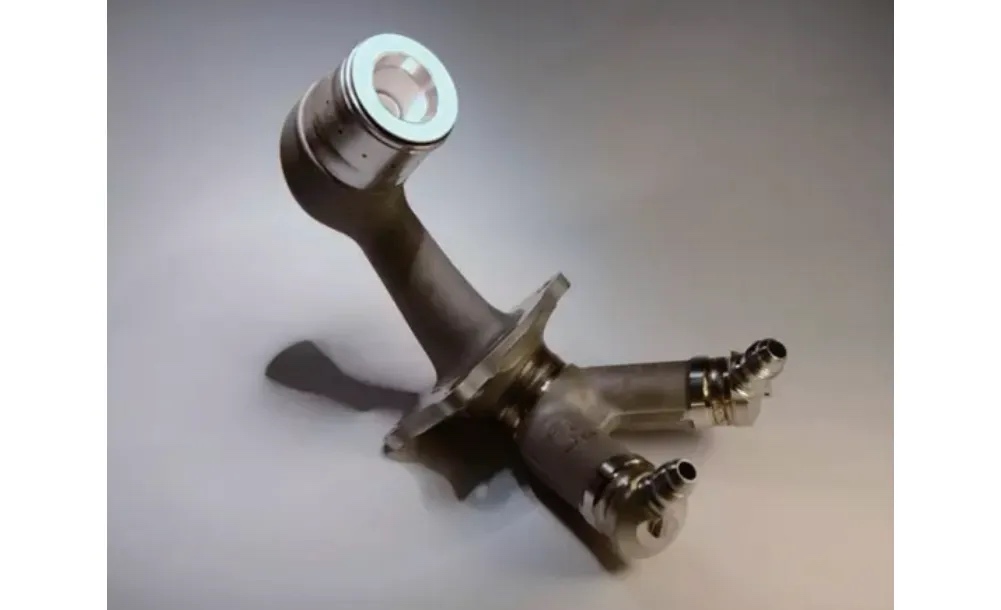
2015年GE公司設在印度Chakan的增材制造工廠開始運營。GE公司希望該工廠最終使GE公司具備每年超過44000個燃油噴嘴的增材制造能力。2016年4月,GE公司斥資4億美元在匹茲堡建設新的增材制造技術發展中心(The Center for Additive Technology Advancement,CATA),希望將其打造成為能夠為設計和應用提供開發服務的創新中心,通過共享其設施,由公司每個事業部來分擔費用,從而整合整個公司的力量,改變各事業部各自投資增材制造、研發效率低下的狀況。CATA將會把精益生產、生產力優化與先進的軟件分析結合起來,用于提升增材制造在整個GE公司內部的創新能力和使用情況。
2016年9月,GE以14億美元收購兩大金屬增材制造設備制造商瑞士 Arcam公司和德國SLM Solutions公司。GE公司計劃通過GE Store模式將增材制造技術用于GE的所有業務。GE公司預計到2020年增材制造業務將增長至10億美元,在未來十年內節約30億到50億美元的成本。
2016年10月27日GE公司宣布以5.99億美元的價格收購德國Concept Laser公司75%的股份。GE公司將在航空航天、醫療等領域獲得或者重塑多個平臺的產品銷售渠道。
根據已經披露的GE公司增材制造計劃,很多增材制造的發動機零部件已通過美國聯邦航空管理局(FAA)的認證,并且已經在LEAP發動機上使用。GE航空公司將進一步在旗下最先進渦輪螺旋槳發動機(ATP)上應用增材制造零部件。通過增材制造技術,將傳統工藝所需的855個零件(占到總零件數的35%)減少為12個。可以通過增材制造的零部件分別是:機油箱、軸承座、框架、排氣機匣、燃燒室、熱交換器和固定流通組件等,該發動機的總壓比將達到16∶1,質量減少5%,油耗將比現在同類型競爭型號低 20%左右,同時返修周期延長30%以上。
英國羅羅公司1994年開始與英國Crankfield大學一起探索航空發動機機匣的激光直接沉積技術。2008年初,羅羅公司宣布與GKN航宇公司(GKN Aerospace)成立一家合資公司,目的在于為下一代發動機提供低成本的發動機風扇葉片,其中增材制造技術將得到大規模應用。2015年羅羅公司通過與英國制造技術中心(MTC)所屬的新國家增材制造中心合作,利用增材制造打印出了有史以來最大的增材制造發動機組件——遄達XWB-97發動機直徑1.5 m的鈦合金前軸承,組件包含的48個翼型導葉也采用增材制造技術生產。羅羅公司2016年開發出自動化的渦輪葉片激光增材制造工藝流程,該流程可以實施小的系列生產。
2016年羅羅公司和GKN航宇公司達成協議,擴展雙方在遄達XWB-84發動機項目上的合作, GKN負責為XWB-84發動機設計供應高性能中間級壓縮機匣(圖6)。該機匣采用包括增材制造工藝和新的焊接技術等最新設計方法和制造技術。首件產品于2018年初交付。Trent XWB-84動機用來為空客A350 900飛機提供動力,計劃于2020年初投入使用。
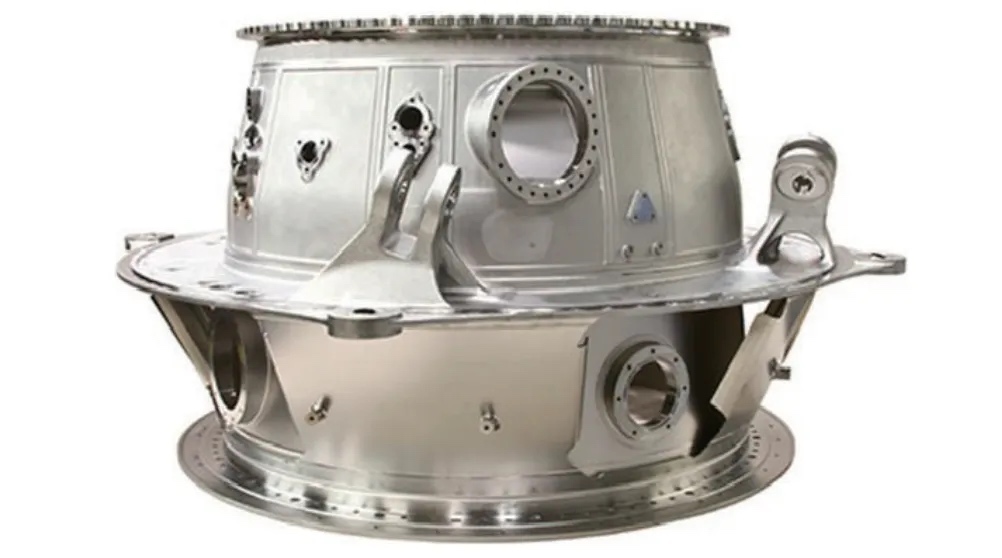
與很多大型科技企業不同,羅羅公司自身很少從事基礎理論研究工作,而是依賴與世界頂級大學建立的協同創新體系,即大學技術中心網絡。普惠公司主要將增材制造用于塑料部件的制造,作為金屬部件的原型和型芯等工藝輔助器材。迄今為止已經制造了超過10萬件原型零件,僅在Pure Power齒輪傳動式渦扇發動機的開發過程中就使用了數百個增材制造零部件的原型。普惠公司采用激光選區熔化制造了PurePower PW1100GJM 發動機的管道鏡套筒,可直接使用管道鏡檢查渦輪殼體和葉片的磨損和損壞狀況。在PurePower齒輪傳動式渦扇發動機開發過程中,使用增材制造技術生產了壓縮機定子和同步環支架。幾十件增材制造鈦金屬和鎳金屬部件已經通過飛行測試并將應用于龐巴迪和空客飛機。
印度INTECH DMLS公司通過SLM增材制造技術為印度斯坦航空公司(HAL)生產25KN發動機燃燒室機匣。首個增材制造的燃燒室機匣已交付給HAL公司,并通過了用戶性能測試。
2019年1月,金屬增材制造部件在F-22猛禽上得到應用。猶他州希爾空軍基地的倉庫維修車間第574飛機維修中隊在F-22猛禽上安裝了一個金屬增材制造部件(飛機支架)。增材制造能夠在短時間內獲得維修更換部件,不再需要訂購。這不僅節省費用,而且減少飛機的維修時間。激光選區熔化的飛機支架不會被腐蝕,從訂購到交付至倉庫再到安裝最快需要三天。此外,維修人員還會使用增材制造的部件來替換駕駛艙總成中易腐蝕的鋁部件,至少還有5個金屬增材制造部件計劃在F-22上進行驗證。如果能夠打印更復雜的部件,可能會使飛機的維修時間減少60~70天。
美國宇航局馬歇爾航天飛行中心、格林研究中心、阿姆斯特朗飛行研究中心正在與維珍軌道公司合作開發和測試增材制造的火箭發動機燃燒室部件。他們的目標是制造一個燃燒室,結合多種材料,并利用先進的制造工藝。傳統的燃燒室制造、測試和交付周期需要數月時間。采用增材制造技術,交付周期將會大大縮短,并為發動機零部件提供新的設計理念和制造機會。維珍軌道公司使用了增/減材混合機床對零部件進行制造與精加工。在2018年末和2019年初,使用高壓液氧/煤油推進劑對燃燒室進行了測試。在近24次60s的測試發射中,該實驗裝置成功地提供了超過8890N的推力。
2019年7月,美國Carpenter技術公司和比利時BMT航空航天國際公司合作開發了一種金屬增材制造航空齒輪。零件由Carpenter技術公司的業務單位 Carpenter 增材制造公司生產,使用其高強度的定制465®不銹鋼增材制造而成。該產品的合作研發表明,在原材料、生產、驗證和設計方面的合作能夠迅速將具有潛力的新產品實現商業化。
2019年8月,發動機制造商Cobra Aero與英國金屬增材制造公司 Renishaw合作,成功優化了飛機和摩托車發動機的設計流程。Cobra的團隊與Renishaw的工程師合作,優化了一種無人機發動機氣缸的設計。重新設計的部分是一個用來改善氣流的復雜網格結構,并將各種組件合并成一個單個輕質部件。通過使用金屬增材制造,Cobra Aero能夠生產出具有復雜晶格結構的單一部件,性能優于傳統制造技術生產的組件。Cobra Aero公司預判,金屬增材制造將成為其主導制造方法。
據美國空軍實驗室2019年8月22日消息,AF-9628鋼的增材制造零件在極限抗拉強度方面比傳統增材制造合金提高20%左右。AF-9628是一種高強度和高韌性的合金鋼,也叫Rachel鋼,它不含鎢,比Eglin鋼和HP-9-4-20 等其他一些高性能鋼合金的價格更低;但它比常規彈藥中使用的普通等級鋼更昂貴。美國空軍實驗室的研究確定AF-9628是增材制造的最佳材料。其增材制造的力學性能好,沒有發現裂紋的跡象,與傳統制造的部件非常相似。在強度增加的同時并沒有變脆,滿足10%伸長率要求。采用激光選區熔化制造的復雜零件,包括幾個復雜的彈丸、鋼瓶。制造的零件適合于武器應用,能夠使未來的穿透武器具有理想的爆炸外形,最終用于制備質量更輕的彈藥,使飛機可以攜帶更多的武器。
3國內激光增材制造技術發展現狀和趨勢
3.1 工藝研究
3.1.1 激光選區熔化工藝研究
西安交通大學在激光增材制造技術的基礎研究、裝備制造、相關軟件開發以及技術應用等方面展開全方位研究,尤其是在應用方面展開深入研究,已將激光增材制造技術應用于快速模具制造、汽車零部件制造等技術領域。并且為其在航空空心渦輪葉片、航天發動機推進器等核心零部件制造方面的應用作了基礎準備。除此之外,還在陶瓷材料的激光增材制造基礎研究和技術應用方面展開大量深入的研究,取得了豐碩的研究成果。
西安鉑力特激光成形技術有限公司現已掌握了鈦合金、鋁合金、高溫合金等材料增材制造工藝,組織和性能數據庫完備。流道類零件可成形的小孔直徑最小僅為0.3mm左右,且能保證孔和流道的流通性;薄壁零件的最小薄壁尺寸約為0.2mm,大面積薄壁的尺寸精度可以控制在±0.3mm左右;整體成形零件的整體尺寸精度基本上可以達到±0.2mm,粗糙度可達 Ra3.2μm以下。無論是工藝技術還是裝備水平,鉑力特公司都已經邁入工程化應用階段。
華中科技大學研發出系列增材制造專用材料制備方法,并實現產業化,包含聚合物、金屬、陶瓷、鑄造型(芯)等材料及其復合材料,研發了系列材料制備成形一體化工藝與裝備,包括建立材料制備成形一體化的數字化表達方法、發明材料制備成形一體化過程多狀態測量與形性調控方法、國際獨創多材料激光3D打印一體化制備成形工藝與裝備等。
中國航發北京航空材料研究院系統開展了激光選區熔化用鈦合金和鋁合金超細粉在飛機復雜結構上的工程化應用研究,積累了粉末特性評價、增材成形工藝、成形后熱處理與熱等靜壓、無損檢測、冶金組織和缺陷分析、力學性能測試、零件性能驗證等各環節的研究經驗和基礎數據。針對航空發動機燃油噴嘴、預旋噴嘴、渦流器、軸流機匣、軸承座、整體導向器、渦輪葉片、管接頭、阻尼環等典型復雜結構,采用常規鑄造高溫合金、鋁合金、鈦合金、不銹鋼以及鈦鋁金屬間化合物、單晶高溫合金、鈮硅超高溫合金等各種材料,深入開展粉末成分設計和粉末制備、激光選區熔化工藝、后處理及組織性能等研究,試制出十多種典型零件,為激光選區熔化技術在航空發動機上的應用奠定了基礎。
南京航空航天大學以選區激光熔化(SLM)精密增材制造技術為主線,開展了航空航天難加工金屬材料構件激光精密增材制造應用基礎研究,在激光精密增材制造裝備研發、專用金屬粉末設計制備、激光成形工藝及機理、高性能復雜金屬零件控形與控性等方面積累并凝練了關鍵技術及科學理論,實現了激光成形零件綜合性能提升及實際工程應用。
北京星航機電裝備有限公司掌握了鈦合金、高溫合金、鋁合金等材料的增材制造工藝,重點突破了TA15鈦合金、GH99高溫合金激光選區熔化成形工藝技術,形成了金屬粉末原材料、產品制造、檢測規范等多項企業標準。
大連理工大學針對增材制造鋁合金異形群孔格柵結構外表面和內孔表面磨粒流拋光,設計了格柵件磨粒流加工夾具,建立了內外表面一體化磨粒流拋光技術方案,采用混合磨粒進行格柵表面和內孔均勻一體化加工,磨粒介質采用含有 24#(20%)、80#(80%)SiC混合磨粒介質。不僅有效去除了格柵表面附著的金屬球、粉末顆粒,而且顯著降低了工件表面粗糙度值。
中國科學院金屬研究所致力于增材制造用高溫合金粉末、鈦合金粉末等高性能金屬粉末的研發及成形構件組織性能調控技術研究,開發出激光增材制造專用高溫合金粉末、鈦合金粉末等材料,突破了激光選區熔化成形技術用超細鈦合金、高溫合金粉末的潔凈化制備技術,粉末特性達到國外進口粉末水平。
西安歐中材料科技有限公司專業從事金屬球形粉末及制件生產與服務。針對激光增材制造的球形金屬粉末生產部署了國際先進水平國內首條超高速 (30000r/min) 等離子旋轉電極霧化SSPREPTM金屬球形粉末工業化生產線。在鈦合金和高溫合金球形粉末制備技術、PREP設備裝置設計優化等方面擁有核心技術100余項。粉末產品通過了中國航發商用發動機有限責任公司、航天材料及工藝研究所等20余家航空航天單位供方評審。
3.1.2 激光直接沉積工藝研究
北京航空航天大學在飛機鈦合金大型主承力結構件激光快速成形工藝研究、工程化成套裝備研發與裝機應用關鍵技術攻關等方面取得突破性進展,提出大型金屬構件激光直接成形過程“ 內應力離散控制” 的新方法,解決了大型金屬構件激光快速成形過程翹曲變形與開裂的“ 瓶頸難題” ,突破了激光快速成形鈦合金大型結構件內部缺陷和內部質量控制及其無損檢測關鍵技術,飛機構件綜合力學性能達到或超過模鍛件。
西北工業大學團隊采用激光增材制造技術打印了最大尺寸3m、質量達196 kg的飛機鈦合金左上緣條。該成品在放置了一個月之后,最大變形量小于 0.8mm,表明其成形精度和變形控制都達到了很高的技術水平。
沈陽航空航天大學提出基于分區掃描成形的激光增材制造工藝方法(圖 7)。通過反饋沉積層面溫度分布,動態規劃激光掃描軌跡,顯著減小沉積過程溫度梯度,降低熱應力、約束應力和晶格儲存能,離散成形過程的殘余應力,有效地控制了沉積過程零件的變形和開裂。
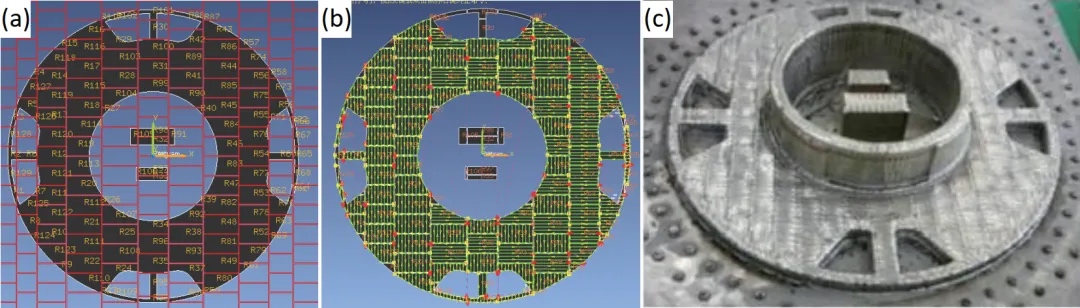
有研工程技術研究院有限公司開展了鈦合金整體葉盤激光修復、激光增材制造Ti2AlNb基合金開裂控制及組織性能調控、TC11/Ti2AlNb 雙合金整體葉盤及TA15/Ti2AlNb異種材料進氣道一體化成形研究,突破了修復界面、異種材料界面質量控制及復雜外形一體化控制難題,激光修復的飛機鈦合金整體葉輪及不同材料飛機部件獲得實際應用,激光增材制造的TA15鈦合金薄壁進氣道通過地面試驗考核。
北京航空材料研究院是中國航空發動機集團增材制造技術創新中心依托單位。掌握粉體材料成分設計和控制技術,擁有較為完善的粉末性能檢測體系。采用激光直接沉積增材制造的鎳基雙合金渦輪整體葉盤通過超轉試驗考核,增材修復的伊爾76飛機起落架獲得批量應用。研制出3D打印制件超聲掃查與評價系統,建立了檢測標準與對比試塊。成果應用于飛機型號裝機件批量檢測,累計檢測滑輪架、框架、短梁等增材制造零件近500件。對增材制造材料力學行為表征與評價、損傷失效分析形成了一整套組織性能損傷關聯性研究、疲勞定量化分析以及壽命預測的理論、技術和方法集成。
3.2 激光增材制造設備
3.2.1 激光選區熔化設備
西安鉑力特激光成形技術有限公司自主開發了激光選區熔化成形裝備系列 BLT-S300和BLTS200,激光高性能修復系列BLT-C600和BLT-C1000。其中S300型設備通過CE認證。公司累計交付各類增材制造設備60余臺,廣泛應用于航空、航天、船舶、兵器、核工業、汽車和醫療等領域。
湖南華曙高科技有限責任公司主攻增材制造主流技術——選擇性激光燒結/選區激光熔融裝備制造、材料生產和加工服務,持續開展高頻度自主創新與實踐,先后研制出全球最快、唯一可燒結PA6材料和開源可定制化的7型 11款高分子、金屬材料工業級增材制造裝備,以及20余款增材制造專用高分子及金屬粉末材料。華曙的所有設備均采用開源性系統平臺,客戶可根據自身需求調整系統參數,還可以利用華曙設備進行二次研發,開發新的材料、工藝及應用。
北京星航機電裝備有限公司在增材制造設備研發方面,實現光路系統設計、高精度運動控制、設備電氣控制等一系列技術突破,完成8臺工業級、3臺小型金屬SLM設備小批量生產;在非金屬增材制造設備方面,研制生產 2臺500mm非金屬SLS設備,及1臺700mm非金屬SLS設備。
北京易加三維科技有限公司專注于研發、生產制造工業級SLS、SLM和 SLA型3D打印設備,聚焦于工業3D打印裝備并圍繞3D打印工藝應用的加工服務業務和產業應用,與傳統制造和桌面型3D 打印形成差異化。目前已經成功開發出金屬材料打印、工程塑料材料打印、砂型及蠟型材料打印、光敏樹脂材料打印等 5 大系列、20 余種機型的產品鏈條。
北京工業大學2014年研發出國內首臺基于DLP技術的面曝光3D打印設備,并通過北京市科委的驗收。2016年開發出基于粉末床技術的金屬3D打印設備。
上海航天設備制造總廠有限公司研制出鋪粉型激光選區熔化增材制造設備,經過多代迭代已經形成成熟的市場型型號。先后研制了多激光束金屬熔化增材制造設備(成形空間250mm×250mm×250mm)、標準型激光選區熔化增材制造設備(成形空間250mm×250mm×280mm)、大幅面選區熔化增材制造設備(成形空間350mm×350mm×300mm)。此外,鑒于國外數據處理軟件以及控制軟件對用戶處于封閉狀態,用戶無法根據工藝研究需求對其中的相關工藝參數進行更改,團隊自主研發了基于三維數字模型分層切片處理軟件及全流程金屬增材制造設備控制軟件。
3.2.2 激光直接沉積設備
南京中科煜宸激光技術有限公司自主研發6kW光纖激光器、全自動變焦同軸送粉噴頭、高穩定長程送粉器、高效惰性氣體循環凈化箱體等核心器件,形成具有自主核心知識產權的高性能合金激光定向能量沉積3D打印系列化裝備,包括:LDM 2020、LDM 8060、LDM 1500、LDM 4000,并成功實現航空航天整體葉盤、起落架等結構件及汽車發動機的3D打印制造。
上海航天設備制造總廠有限公司研制出機器人型同軸送粉激光直接沉積增材制造設備(成形空間1500mm×1200mm×900mm)。團隊自主研發了基于三維數字模型分層切片處理軟件及全流程金屬增材制造設備控制軟件。
3.3 技術應用
激光直接沉積主要應用于承載結構件的研發和小批試制。
北京航空材料研究院將激光直接沉積技術應用于伊爾76飛機超高強度鋼起落架作動筒修復,修復的前起作動筒經900h起落飛行,狀態良好,修復的起落架已實現批量應用。激光直接沉積修復的伊爾76飛機襟翼滑軌、環控導管,軍用飛機端軸頸、搖臂、螺栓、扭力臂,以及民航飛機轉軸、閥芯等零件也實現了批量應用。此外,將激光選區熔化應用于航空渦軸發動機導向葉片高溫合金導流管的成形制造,并實現了批量應用。
中國航空制造技術研究院激光選區熔化技術在國內率先實現裝機應用,并于2014年先后向航空、航天、兵器等行業領域推廣應用。
航空工業成都飛機設計研究所通過設計及需求牽引,組織國內優勢單位聯合攻關,將激光選區熔化成形的發動機艙進、排氣門格柵結構應用于某型飛機。
沈陽飛機設計研究所基于設計/制造一體化新概念結構創新技術研究,通過結構設計牽引激光增材制造技術發展,通過工程化應用驗證促進技術成熟度的提升,實現了8種金屬材料、10類3D打印制造結構件(框、梁、肋、接頭、耳片、起落架)在4個飛機型號或項目中的應用。
航空工業第一飛機設計研究院經過近10余年的自主設計和創新,在飛機大型整體鈦合金主承力結構件激光增材制造及裝機應用研究方面取得突破性進展,大型飛機鈦合金外主襟翼滑輪架、尾翼方向舵支臂兩個零件得到裝機應用。
航空工業直升機所在直升機前期設計階段,吹風模型、駕駛艙人機功效模型等大量采用激光3D增材制造技術完成數模加工。通風格柵結構、淋雨密封結構、進氣道多腔體結構等功能結構及復雜外形結構件已實現3D打印加工制造及裝機,某些主受力結構件,如起落架、多管路輔助接頭也進行了 3D打印預先研究。
2005年來,北京航空航天大學研制生產了飛機機身主承力框、翼身根肋、主起落架等100余種大型整體鈦合金及超高強度鋼承力關鍵構件,在我國艦載機、大型運輸機、C919大型客機、四代機等7個重點型號飛機及大型運載火箭等5型火箭/導彈、新型衛星、燃氣輪機/汽輪機等10多型重大裝備研制和小批量生產中得到實際應用。
除航空領域外,激光直接沉積技術還應用于航天等行業。
西安鉑力特激光成形技術有限公司針對航空航天極端復雜的精密構件加工制造問題,利用SLM技術,解決了隨形內流道、復雜薄壁、鏤空減重、復雜內腔、多部件集成等復雜結構問題,每年可為航空航天領域提供復雜精密結構件8000余件。
鑫精合激光科技發展(北京)有限公司采用激光選區熔化技術自主研發制備了大尺寸薄壁鈦合金點陣夾層結構件——集熱窗框,滿足了火星車產品的技術要求,保障了火星車產品的順利研發與實驗。
上海航天設備制造總廠有限公司采用激光增材制造技術制造的火箭箱間斷支架、衛星散熱器、導彈導引頭關鍵零件等產品,已實現型號應用。
北京星航機電裝備有限公司在產品結構優化設計、創新成形工藝、復合增材制造等方面開展了深入的工藝技術驗證,積極推動增材制造技術在航天艙段類結構件、舵面產品上的應用,部分產品通過地面試驗及飛行試驗驗證。
北京機電工程研究所已實現大尺寸薄壁骨架艙段結構的激光直接沉積和小型復雜零部件的激光選區熔化制造,提高了產品的研發效率,縮短了研發周期。目前相關產品,包括舵面翼面、支架等的技術成熟度達到5級。
華中科技大學激光增材制造技術在多家企業得到應用,提升了傳統制造業水平,效果顯著。通過增/減制造具有隨形冷卻水道的梯度材料模具,保證了模具的整體性能,成果在廣東科龍模具和湖北三環鍛造等企業應用,內嵌冷卻水道的注塑模硬度提高2倍、冷卻周期縮短68%以上,模具使用壽命提高3倍,再制造模具成本僅為重新制造的10%。
3.4 國內外激光增材制造重點領域的技術
發展趨勢研判
增材制造材料和零件的性能要求不斷提高,推動激光增材制造工藝方法不斷發展豐富。增材制造的材料由固溶強化高溫合金延伸至固溶時效高溫合金,由普通鈦合金延伸至高溫鈦合金、鈦鋁金屬間化合物,由單一金屬材料延伸至金屬基/陶瓷基復合材料、梯度材料。增材制造的零件由次承載、功能結構向承載、結構功能一體化結構發展,零件增材組織由等軸晶向定向凝固、單晶組織發展。“ 材料-結構-性能一體化增材制造” 整體性概念開始被接受,并引導增材制造走向材料-結構-工藝-性能一體化“ 并行模式”。材料性能提高,伴隨增材制造工藝性降低;零件組織性能提高,伴隨增材制造難度增大;這些都催生多能量場、多物理場增材制造新工藝的發展。由于航空領域對激光增材制造結構的高可靠、長壽命要求,在一定程度上會制約其在飛機、發動機關鍵部位的應用。可以推測,增材制造發展重點必然會轉向增材制造產品的冶金質量、力學性能及其穩定性控制方面。另外,基于增材制造技術,設計制造一體化開發的散熱器 、 框梁等新型結構開始應用于飛機制造。激光選區熔化制造復雜、輕質、新型次承力或功能性結構也會成為國內外增材制造技術的重要發展方向。
在設備方面,增減材復合加工設備和技術成為一個重要發展方向,對于提高制造效率、降低制造成本會產生重要影響。大尺寸、超大尺寸激光選區熔化設備正在成為國內外設備制造商競相開展研發的增材制造設備。增材制造設備的智能化,包括在線監測、參數自整定控制等功能的研究開發,正成為增材制造設備的研發熱點。尤其是激光增材制造的熔池動態監測、粉末床和熔融層的可見光檢測技術,近年來發展迅速,其中熔池動態監測已應用于工藝反饋控制。
在增材制造制件評價技術方面,針對增材制造組織、結構開發專門的超聲波、工業CT技術是一個重要研究方向。基于損傷失效分析、壽命預測研究的增材制造結構力學行為研究,以及基于元件、單元體和特征結構的結構使用性能考核驗證技術研究,正在引起越來越多的關注。
4航空裝備激光增材制造路線圖研究
4.1 2035 年發展目標
4.1.1 需求
激光增材制造基于數模切片通過逐層堆積實現零件近凈成形制造,無需模具,節省材料,縮短研制和生產周期,降低制造成本。特別適合復雜形狀零件、梯度材質與性能構件、復合材料零件和難加工材料零件的制造,還支持結構設計創新和結構功能一體化制造。
航空航天領域的零件,外形復雜多變,材料硬度、強度等性能要求較高,難以加工且成本較高。而新生代飛行器正在向高性能、長壽命、高可靠性以及低成本的方向發展,采用整體結構、復雜大型化是其發展趨勢。正是基于此發展趨勢,激光增材制造技術越來越受到航空航天制造商的青睞。
航空發動機燃油噴嘴、軸承座、控制殼體、葉片等零件,內部具有復雜油路、氣路和型腔,為提高效能而進行結構創新設計,更增加了結構的復雜性和制造難度。飛機發動機艙進、排氣門格柵結構,武器艙的艙門支座等部件,結構非常復雜,這些新型復雜構件的成形對基于激光選區熔化的增材制造技術具有迫切需求。
航空發動機各類機匣、壓氣機/渦輪整體葉盤、尾噴調節片等結構,形狀復雜,為提高效能甚至需采用異種或梯度材料結構。
飛機超高強度鋼和不銹鋼接頭、滑軌、起落架,鋁合金承力框、梁,鈦合金框、支座、滑軌、滑輪架、筋壁板等承力構件,高馬赫飛行器翼舵格柵結構承載骨架,為提高減重和承載效能須進行拓撲優化結構創新設計,結構的復雜性和制造難度增加,采用傳統工藝制造難度大,對激光直接沉積增材制造具有明確技術需求。
高推重比發動機渦輪進口溫度的提高,要求采用超高溫金屬間化合物以及金屬基/陶瓷基復合材料等新型高溫結構材料。新型高溫/超高溫材料零部件的研制對激光增材制造技術提出了潛在需求。
飛機、發動機某些帶局部凸臺、耳片等特殊結構的承力構件,采用鍛造工藝無法保證局部組織和性能;大型飛機的超大規格鈦合金承力框,超出現有鍛造設備的加工能力。對鍛造+增材制造/增材連接的復合制造技術具有明確技術需求。
激光增材制造技術經過近年的項目支持,基本解決了原材料、成形工藝、復雜零件制造等關鍵技術,開始獲得應用。目前制約激光增材制造大規模應用的瓶頸之一是疲勞問題。需要特別重視激光增材制造疲勞問題的原理性研究。
為了提高航空產品激光增材制造的工藝過程穩定性和質量,需要發展基于熔池動態監測、粉末床和熔融層可見光檢測的在線監測、檢測技術。
航空領域對激光增材制造的需求主要體現在以下幾個方面:
(1) 飛機鈦合金框梁重要承力結構高性能高可靠激光直接沉積;
(2) 飛機超高強度鋼起落架抗疲勞長壽命激光直接沉積;
(3) 飛機鈦合金、鋁合金格柵點陣復雜結構激光選區熔化;
(4) 航空發動機燃油噴嘴類零件激光選區熔化;
(5) 航空發動機渦流器、葉片類零件激光選區熔化;
(6) 航空發動機控制、附件殼體類零件激光選區熔化;
(7) 航空發動機機匣、軸承座類承力零件激光選區熔化;
(8) 航空發動機整體葉盤/機匣類承力零件激光直接沉積;
(9) 飛機、發動機超大規格結構鍛造+增材制造/增材連接的復合制造;
(10) 激光增材制造疲勞問題的原理性研究;
(11) 激光增材制造過程的在線監測、檢測技 術研究。
4.1.2 目標
突破飛機、發動機材料激光增材制造缺陷、組織、力學性能控制關鍵技術,掌握粉末設計與制備技術,制定材料、工藝、檢測標準,建立工藝、性能數據庫和冶金圖譜,掌握零件產品質量控制技術,制定零件產品技術標準。在產品增材制造質量控制技術、產品技術標準研究和零件充分考核驗證的基礎上,推進激光增材制造在航空、航天、船舶、核工業等重點制造領域的應用。至2035年,在航空領域普通金屬激光增材制造全面量產應用;金屬間化合物增材制造的組織-性能-變形控制技術全面突破,性能驗證基本完成,功能考核部分完成,部分產品進入量產。鈮-硅、陶瓷基材料增材制造物理冶金原理得到揭示,性能驗證基本完成,部分產品開始裝機應用。
4.2 2035年發展路線圖
4.2.1 重點產品
(1)飛機:
鈦合金框梁重要承力結構;超高強度鋼起落架外筒;鈦合金、鋁合金格柵點陣復雜結構。
(2)發動機:
航空發動機燃油噴嘴類零件;航空發動機渦流器、葉片類零件;航空發動機控制、附件殼體類零件;航空發動機機匣、軸承座類承力零件;航空發動機整體葉盤/機匣類承力零件。表2為2035年航空領域激光增材制造技術發展路線圖。
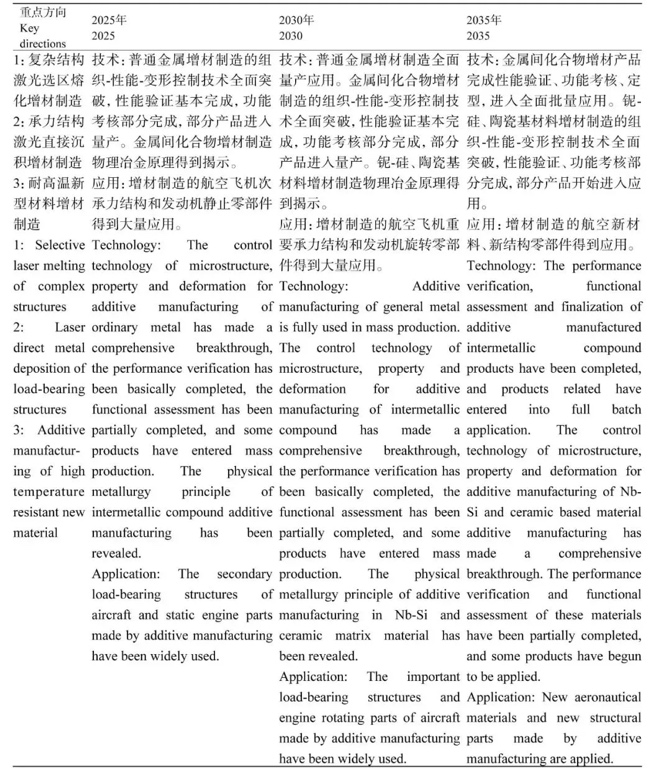
4.2.2 關鍵共性技術
(1) 激光選區熔化用高品質粉末成分設計與制備技術
激光增材制造成形制件的組織與鑄件、塑性成形件具有顯著差別,為獲得相當的性能水平,通常需要對材料成分進行設計調整,即開發適合增材制造的專用材料。為獲得良好的成形工藝性、優良的制件內部和外部質量,激光選區熔化增材制造工藝對所采用的粉末原材料的質量,如粉末的球形度、空心粉率、氣體含量、夾雜率、粒徑分布、流動性等,均提出嚴格的要求。加之所采用的材料為了提高力學性能,均采用特殊的成分體系,導致其液態和固態塑性加工性能較差。這些都增加了高品質粉末制備的挑戰性。
(2) 激光增材制造的缺陷控制和組織性能改善技術
飛機、發動機優良的綜合性能的獲得,通常以犧牲材料的熱加工性為代價。用于燃油噴嘴、渦流 器等零件的高溫合金、鈦合金、鋁合金、馬氏體不銹鋼等材料,在凝固過程中,發生裂紋的傾向性普遍較高,容易導致制件報廢,或嚴重降低制件的可靠性。對于鈦合金的增材制造,產生氣孔的概率很高。增材制造采用逐層堆積,如工藝參數選取不合適,容易在層間產生未熔合或熔合不充分等缺陷。飛機重要承力結構,要求長壽命、抗疲勞、高可靠。發動機熱端部件還對持久、蠕變等性能提出了要求,這就要求對增材制造的組織形態進行嚴格的控制。因此,需要通過工藝優化及合適的后續處理,防止缺陷產生、獲得優良組織,保證制件性能。由于工藝參數的調整,對于不同性質缺陷的產生、組織形態和力學性能的變化等所產生的影響十分復雜,最優的工藝窗口可能很窄,必須經過實質上的一個多目標優化過程才可能確定。
(3) 復雜結構精確成形的增材制造應力變形控制技術
增材制造過程的逐層堆積引起熱應力和變形的累積。每層材料的熔融、凝固均會產生一次凝固收縮。因此,增材制造的制件內部存在較大的應力,這會引起制件開裂或宏觀變形。對于飛機框梁、起落架等大投影面積、大厚度結構,以及發動機燃油噴嘴、渦流器、機匣等復雜、薄壁結構,應力變形問題更為突出,導致制件外觀尺寸和內部通道等形狀控制難度大為增加。因此,需要通過優化制件的空間擺放,采用合適的沉積策略、工藝支撐,優化成形工藝參數、采用合適的預熱及后熱處理,才能實現對應力變形的有效控制。
(4) 激光選區熔化成形復雜結構的評價與測試技術
激光增材制造技術應用于飛機重要承力和功能結構,其內部缺陷、組織特點不同于鍛造、鑄造結構,導致傳統的檢測、評價方法和技術標準未必適用。激光增材制造技術應用于發動機燃油噴嘴、渦流器、軸承殼體等帶內部流道或者中空薄壁類的復雜結構,這些結構的內部流道角度、形狀和尺寸公差、表面粗糙度,對結構功能均有重要影響;但是這些結構特征采用常規的檢測技術難以檢測,必然會對增材制造技術的推廣應用造成限制。由于激光選區熔化成形材料及結構的組織、缺陷有其特殊性,常見的氣孔、未熔合、裂紋等缺陷的尺寸僅為微米量級,采用常規的方法難以檢測,另外,材料的組織特征及缺陷的類型、尺寸、分布等對結構的力學性能、可靠性和使用壽命影響還缺乏系統性研究。這些問題嚴重限制了激光增材制造技術在航空領域應用。
(5) 增材制造元件級及零件級力學性能考核
由于增材制造與傳統的鑄造、鍛造組織缺陷存在明顯差異,使增材制造構件的力學性能及其斷裂行為存在顯著不同。對于增材制造整體葉盤,如何表征材料及整體葉盤的力學行為也是亟待解決的科學問題之一。增材制造整體葉盤的力學行為研究,包括增材制造材料力學行為、元件級(單元體)力學行為、零件典型件力學行為研究。對于單元體力學行為、零件典型件力學行為,國內還沒開展相關研究,國外RR、GE、MTU等機構的研究也鮮有公開報道,仍處于保密階段。
5 結論與建議
(1)增材制造特別適合零件的快速研制、快速驗證和設計改進,并且支持結構設計創新,因此在飛機鈦合金承力框、滑輪架和超高強度鋼起落架外筒等重要承力結構以及飛機艙門連接件、輔助動力艙進氣門、排氣門格柵結構、武器艙門支座、橫梁等復雜結構的制造中得到應用,在航空發動機燃油噴嘴、渦流器、渦輪葉片、傳感器殼體、燃油控制系統殼體等復雜結構的制造中也得到批量應用。不僅縮短了零件研制周期,降低了制造成本,而且增加了設計的自由度,通過結構功能一體化設計創新,取得了質量減輕、承載耐溫能力提高、工作效能提高等效果。一方面加快了飛機、發動機的研制進度,另一方面由于采用結構功能一體化制造,大大減少了零件數量,顯著提高了裝備的可靠性。
(2)國內增材制造技術發展仍存在短板和不足,制約著增材制造技術創新及產業化應用。增材制造設備激光器、光路、加工頭等核心器件自主保障能力不足,零件數模切片、掃描路徑規劃、實時監測控制軟件研發能力欠缺,限制了工藝創新的上升空間。對傳統材料和新材料增材制造組織、性能、缺陷、應力變形發展規律的研究不深入,導致制件增材制造的控性控形工藝開發效果不佳。對于粉末、絲材原材料和增材制造工藝過程的質量控制以及制件性能評價研究不充分,導致相關材料規范、工藝標準、檢測方法、產品技術標準的缺失,嚴重制約增材制造的批量化規模化應用推廣。
(3)為推動我國增材制造技術在航空領域的發展和應用推廣,需要從科研項目支持、科研生產條件配套、設備研發能力提升等方面提供全方位的戰略保障。具體建議如下:
① 設立不同類型科研項目支持技術研發
結合在研、在役飛機、發動機型號研制和性能提升,設立型號課題,針對已具備較好研究基礎的TC4鈦合金、AlSi10Mg鋁合金、GH3536高溫合金增材制造技術,支持開展工程化應用研究,解決產品質量控制和產品技術標準關鍵技術,推動技術的規模化量產應用。針對預研飛機、發動機型號研制需求,設立預先研究課題,針對高強高韌鈦合金、高鋁鈦高溫合金等高性能材料增材制造技術,支持開展控性、控形關鍵技術研究,研制典型零件并開展相關考核試驗,推動技術型號應用。面向未來飛機、發動機型號需求,設立應用基礎研究課題,支持開展超高溫結構材料、新型材料、新型結構增材制造技術研究,為新概念航空裝備設計制造儲備技術基礎。
② 配套科研條件建設
根據型號課題、預先研究課題、應用基礎研究課題需要,進行配套科研條件建設,建立各階段研究所需設備、計算機軟件等硬、軟件設施。
③ 支持相關基礎元器件、設備集成、軟件開發
支持提升國內增材制造設備集成能力、重要核心元器件的研發制造能力,支持開展國內數模切片軟件、掃描策略規劃軟件、工藝參數控制軟件、模擬仿真軟件的優化、開發,提高裝備和工藝的智能化水平。
來源:沈陽德為科技、航空材料學報、機械工程材料期刊
作者:王天元,黃 帥,周 標,鄭 濤,張國棟,郭紹慶
工作單位:
1.中國航發北京航空材料研究院
2.中國航發集團增材制造技術創新中心
3.北京市航空發動機先進焊接工程技術研究中心
(責任編輯:admin)